Amid market challenges and increasing unpredictability, supply chain resilience is now essential for businesses aiming to minimize risks and sustain steady production. For companies in manufacturing or those dependent on intricate components, CNC (Computer Numerical Control) machining offers a dependable, flexible solution to bolster resilience across the supply chain.
By optimizing efficiency and ensuring precision, CNC machining can fortify your business against potential supply chain disruptions. At Yijin Hardware, we have extensive experience in providing precision CNC machining services that support businesses in achieving these goals. Below, we outline five ways CNC machining can strengthen your supply chain resilience, providing both immediate and long-term benefits.
1. Increased In-House Manufacturing Capabilities
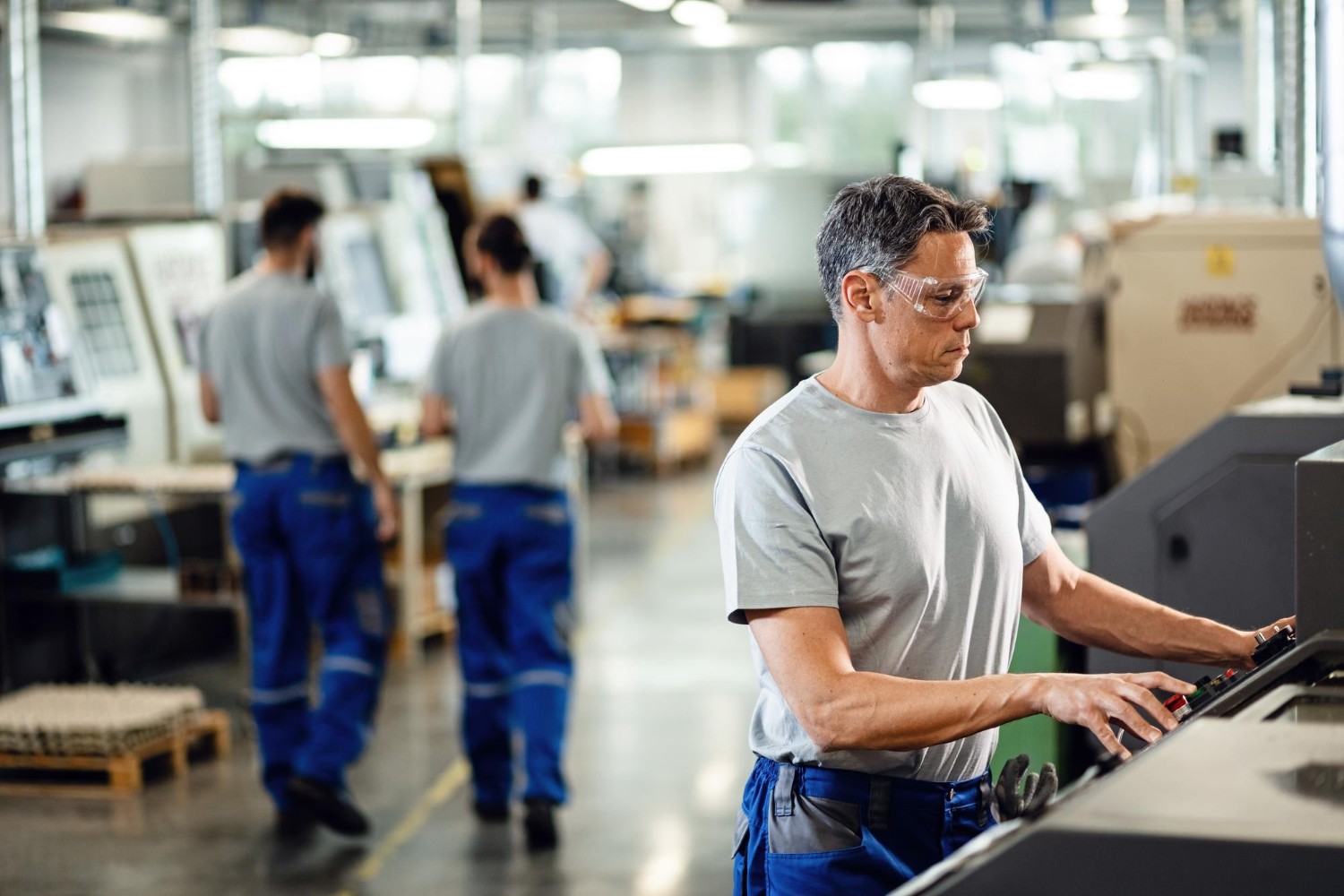
One of the most significant ways CNC machining bolsters supply chain resilience is by enabling businesses to handle production internally. When companies can produce essential components in-house, they minimize dependency on external suppliers, which can be crucial during times of global disruption or supply shortages. For example, CNC machines can produce complex parts on demand, reducing the need to wait for shipments from third-party suppliers or navigate delays in overseas logistics.
By reducing reliance on external manufacturing, businesses can experience:
- Improved production control by monitoring and adjusting manufacturing in real time
- Reduced lead times by eliminating transport and supplier delays
- Enhanced quality control by maintaining oversight of every production stage
Bringing CNC machining in-house also reduces the risk of supplier-related disruptions and helps avoid stockouts, enabling companies to meet customer demands consistently.
2. Flexibility in Design and Production
CNC machining provides unmatched flexibility, allowing companies to quickly adapt their production to new or changing needs. In a resilient supply chain, this flexibility translates to reduced downtime and faster turnaround for urgent production requests. Whether due to shifts in market demand or the sudden unavailability of certain parts, CNC machining can make it easier for companies to change production designs quickly, even with complex geometries or high-precision requirements.
Flexibility in design and production also means:
- Rapid prototyping: CNC machines can produce prototype parts swiftly, enabling quick adjustments and innovation.
- Customizable output: Whether scaling up for high-volume production or creating custom, small-batch components, CNC machines can seamlessly adjust to different production needs.
- Enhanced adaptability: In the face of unforeseen changes in supply chain availability, CNC machining can rapidly shift production to a substitute design or material with minimal downtime.
This adaptability is especially useful in industries that experience frequent shifts in design requirements, such as electronics, automotive, and aerospace. CNC machines can process new designs by updating CAD files, eliminating the need to retool equipment and saving valuable time in meeting shifting demands.
3. Reduced Material Waste and Lower Production Costs
Material efficiency is an often-overlooked component of supply chain resilience, as reducing waste and optimizing resources can significantly buffer a business against fluctuating material costs. CNC machining helps minimize material waste by using subtractive manufacturing, which is more precise and reduces excess scrap compared to other methods. When used strategically, CNC machining enables companies to make the most of their materials, keeping costs down and reducing the impact of material shortages or price spikes.
The cost savings from CNC machining arise in multiple ways:
- High precision with minimal scrap: CNC machines can deliver exact cuts and dimensions, leading to consistent quality with minimal waste.
- Optimized inventory management: With CNC machining, businesses can streamline material procurement by predicting the exact amount of raw material required, helping avoid excess inventory.
- Lower maintenance costs: CNC machines are designed for durability and efficiency, which means reduced wear and tear on parts and fewer unplanned maintenance requirements.
By reducing waste, companies also reduce costs, which allows them to redirect resources into enhancing their supply chain, such as investing in higher-quality materials, ensuring redundant stock, or building stronger supplier partnerships.
4. Improved Quality Control and Consistency
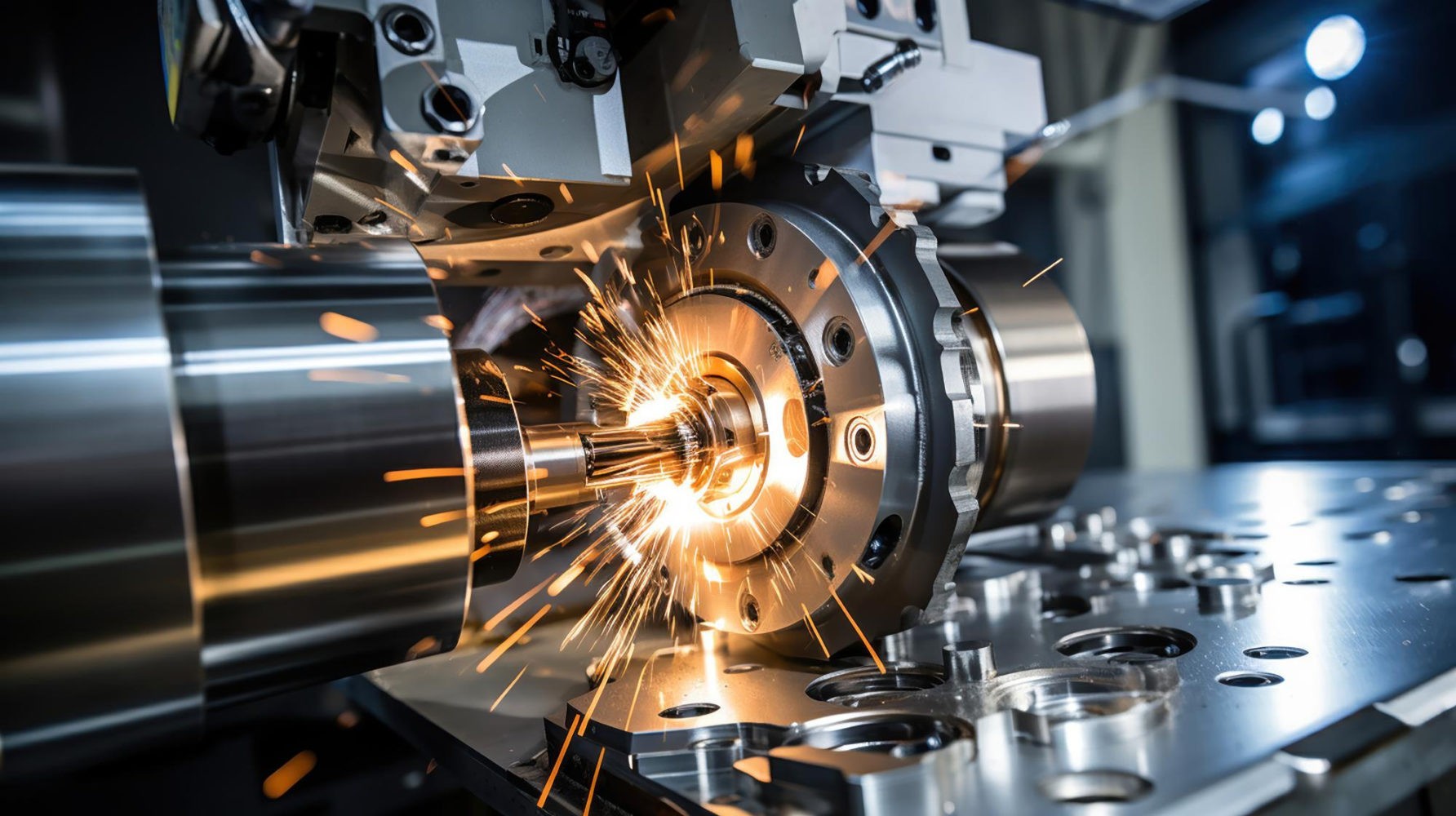
Quality consistency is a cornerstone of supply chain resilience, as high-quality products with minimal defects reduce the risk of returns, recalls, or customer dissatisfaction. CNC machining provides a level of accuracy and repeatability that ensures products meet exact specifications consistently. Unlike manual manufacturing, where human error can introduce variations, CNC machines follow programmed instructions precisely, allowing for consistent quality across all produced parts.
CNC machining enhances quality control through:
- Exact replication: CNC machines operate with high precision, replicating complex parts with little to no deviation, which is essential for products requiring strict tolerances.
- Reduced inspection time: With consistent output, the need for intensive inspection and testing diminishes, accelerating production times.
- Improved durability: CNC-machined parts often exhibit greater structural integrity, which reduces the likelihood of failure in end-use applications and helps maintain a steady flow of products through the supply chain.
By providing reliable, consistent parts, CNC machining can reduce delays associated with quality issues, helping your business maintain smooth production even during peak demand periods.
5. Scalability for Demand Fluctuations
One of the greatest advantages of CNC machining for supply chain resilience is its scalability. Demand fluctuations, whether seasonal or due to unexpected market changes, can be challenging for traditional production methods to accommodate. However, CNC machining systems allow businesses to scale production up or down quickly and efficiently.
Scalability benefits include:
- On-demand production: CNC machines can adjust to varying volumes without extensive retooling, allowing businesses to increase output during peak demand or reduce it during slower periods.
- Efficient resource allocation: CNC systems can run continuously with minimal supervision, allowing businesses to adjust labor and resources flexibly.
- Faster lead times: With the capacity to handle rapid scale-up requests, CNC machining helps meet deadlines without sacrificing quality, even when demand surges unexpectedly.
For businesses experiencing rapid growth or seasonal peaks, CNC machining’s scalability provides a stable production foundation, helping meet customer demands without compromising quality or overextending resources.
Conclusion
In a business landscape increasingly impacted by unpredictable global events, maintaining a resilient supply chain is essential. CNC machining plays a transformative role in building that resilience by empowering businesses to manage production internally, adapt to design changes, reduce waste, and maintain consistent quality. The scalability of CNC machining further allows businesses to respond to demand changes without lengthy retooling or costly delays. By integrating CNC machining into your operations, your business can significantly enhance its supply chain resilience, achieving greater efficiency, cost savings, and quality control that contribute to long-term stability and competitive advantage.
Investing in CNC machining not only equips your business with advanced manufacturing capabilities but also strengthens your entire supply chain to withstand and adapt to evolving market conditions.
⸻ Author Bio ⸻
Elizabeth J. Preston is an experienced writer specializing in business technology, smartphone innovations, and digital transformation. She is passionate about exploring how emerging technologies drive business growth, improve efficiency, and shape the future of industries. Outside of writing, Elizabeth enjoys analyzing market trends, testing the latest tech gadgets, and sharing actionable insights to help businesses thrive in a digital world.