In the race to go green, businesses often overlook a powerful sustainability ally hiding in plain sight: maintenance. Every day, facilities worldwide waste energy, materials, and resources due to inefficient maintenance practices. By incorporating smart maintenance practices, organizations can achieve significant ROI in cost savings, energy efficiency, and resource optimization.
Smart maintenance isn’t just about keeping machines running; it’s about revolutionizing how organizations approach sustainability. By bridging operational efficiency with environmental responsibility, computerized maintenance management systems are transforming sustainability outcomes across industries.
The Evolution of Maintenance: From Reactive to Predictive Intelligence
The journey from fixing things when they break to preventing failures before they happen represents a major leap forward in sustainability. This evolution has redefined how organizations approach equipment care and resource management. The work order management system has played a key role in this shift, enabling teams to track, plan, and execute maintenance more efficiently while minimizing waste and downtime.
With this understanding of how maintenance drives sustainability outcomes, let’s explore how the maintenance landscape itself has evolved from traditional approaches to today’s intelligent systems.
Traditional Maintenance Pitfalls and Environmental Costs
Reactive maintenance approaches come with hefty environmental price tags. When equipment fails unexpectedly, organizations scramble to deploy emergency repair teams, often resulting in:
- Excessive fuel consumption from rushed service calls
- Wasted materials from emergency repairs that might not address root causes
- Higher energy usage from underperforming equipment running inefficiently
The carbon footprint of these reactive operations adds up quickly. Emergency repairs typically require expedited shipping of parts, often via air freight generating 10-30 times more carbon emissions than ground transportation.
Additionally, the hidden sustainability costs of unplanned downtime include scrapped materials, production restarts, and sometimes complete replacements rather than repairs.
The Rise of Smart Maintenance Technologies
Today’s maintenance technologies harness the power of connectivity and data. IoT sensors continuously monitor equipment health, collecting real-time data on vibration, temperature, voltage, and countless other parameters that indicate potential issues before they cause failures.
AI-driven predictive analytics transforms this sea of data into actionable insights. These systems learn from historical patterns to forecast when components might fail, allowing maintenance teams to schedule interventions at optimal times. Cloud-based maintenance platforms enable these capabilities while reducing the environmental impact of on-site servers and paper-based processes.
The shift from reactive to smart maintenance unlocks significant environmental opportunities. Now, let’s examine the five fundamental pillars that form the foundation of truly sustainable maintenance operations.
5 Core Pillars of Sustainable Maintenance Operations
Smart maintenance strategies rest on five key pillars that collectively drive sustainability while improving operational performance. These interconnected approaches deliver both environmental and business benefits.
Energy Optimization Through Preventive Maintenance Scheduling
Well-maintained equipment simply uses less energy. A preventive maintenance scheduling approach ensures that machines operate at peak efficiency, avoiding the energy waste that comes with struggling components or systems.
For example, a properly maintained HVAC system can reduce energy consumption by 15-20% compared to a neglected one. The connection between equipment efficiency and carbon footprint is direct and significant – organizations can slash emissions by simply ensuring equipment runs as designed.
Automation of energy-intensive maintenance tasks further reduces consumption. Smart scheduling routes technicians efficiently to reduce travel, while digital workflows eliminate paper waste from traditional documentation.
Resource Conservation With Intelligent Asset Management
Smart maintenance extends equipment lifecycles dramatically. Data-driven maintenance decisions help organizations get the maximum life from assets without risking catastrophic failures that lead to premature replacements.
Implementing an asset-tracking system allows maintenance teams to monitor component health throughout its lifecycle, minimizing parts consumption and replacement waste. These systems provide real-time visibility into inventory, preventing overordering and underutilization of spares.
Digital twins – virtual replicas of physical assets – allow teams to simulate maintenance scenarios before implementing them, ensuring that the most resource-efficient approaches are selected.
Emissions Reduction Through Strategic Maintenance Planning
A work order management system optimizes maintenance-related transportation and logistics, dramatically reducing emissions from service vehicles. By grouping similar tasks geographically and prioritizing work based on urgency and location, organizations minimize unnecessary travel.
Remote diagnostics capabilities reduce site visits altogether. Technicians can troubleshoot issues and guide on-site personnel without making the trip themselves. This approach not only cuts emissions but also improves response times.
Forward-thinking organizations are also electrifying their maintenance fleets. Electric vehicles for maintenance staff represent a significant opportunity to reduce the carbon footprint of service operations.
Waste Minimization with Precision Maintenance
Targeted interventions based on actual component conditions reduce waste compared to whole-system replacements. Using ultrasonic, infrared, and vibration analysis, technicians can identify exactly which components need attention.
This precision extends to consumables like lubricants and cleaning agents. Smart maintenance systems track usage patterns and recommend optimal quantities, reducing hazardous material waste. Digital documentation eliminates paper waste from work orders, manuals, and reports that traditionally accompany maintenance activities.
Water Conservation in Maintenance Procedures
Maintenance activities often consume surprising amounts of water. Smart cleaning technologies like dry-ice blasting and ultrasonic cleaning significantly reduce this water usage while effectively maintaining equipment.
Water recycling systems capture and filter water used in maintenance processes, allowing it to be reused multiple times before disposal. Advanced leak detection through monitoring systems prevents water waste from equipment malfunctions, which can save thousands of gallons annually in industrial settings.
With these five pillars establishing the framework for sustainable maintenance, implementing the right work order management system becomes crucial for turning these principles into measurable environmental benefits.
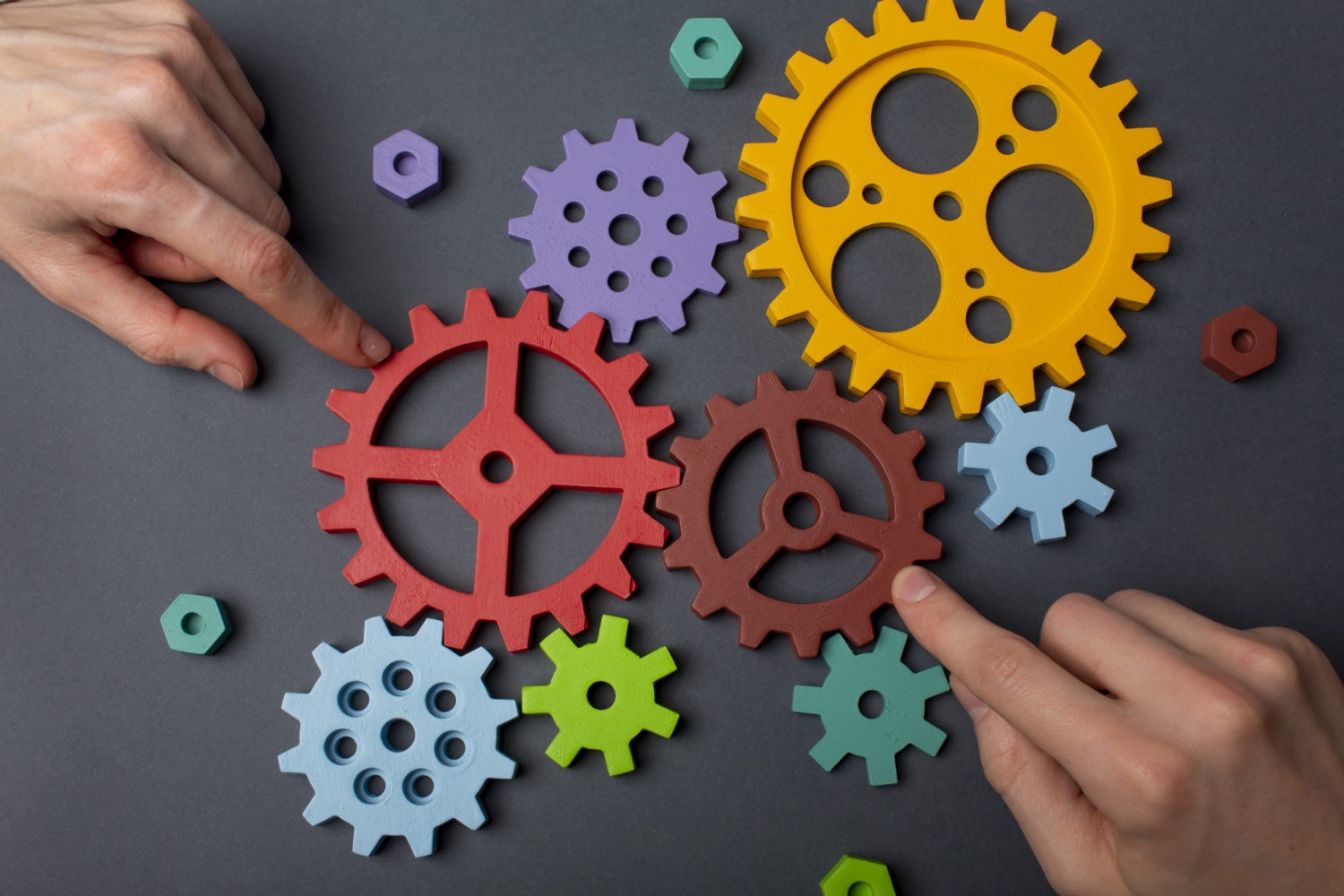
Implementing a Work Order Management System for Sustainable Operations
A robust work order management system forms the backbone of sustainable maintenance operations. These systems streamline processes and provide the data infrastructure necessary for continuous improvement.
Digital Transformation of Maintenance Workflows
Paperless work order processing eliminates thousands of printed documents annually for even modestly sized operations. Beyond the obvious paper savings, digital workflows reduce transportation emissions by allowing remote work order initiation, approval, and completion.
Mobile maintenance solutions put all necessary information in technicians’ hands through smartphones or tablets. This mobility reduces travel requirements and allows teams to complete more work with fewer resources.
Automated prioritization ensures that sustainability-critical tasks receive appropriate attention. Systems can flag work orders affecting energy efficiency, emissions, or resource consumption for expedited handling.
Data-Driven Maintenance Decision-Making
Analytics capabilities help maintenance teams spot patterns that human observation might miss. By analyzing equipment performance trends, organizations can proactively address issues that waste energy or resources.
This data-driven approach also identifies sustainability improvement opportunities. Teams can target the specific machines, processes, or facilities with the highest environmental impact for immediate attention.
Facility management software provides dashboards to measure and track sustainability KPIs. These visual tools help maintenance teams understand their environmental impact and monitor improvements over time.
While effective work order systems create the operational backbone for sustainable maintenance, cutting-edge technologies are rapidly expanding what’s possible in this field.
Equipment Downtime Reduction: The Hidden Sustainability Opportunity
Equipment downtime reduction represents one of the most overlooked sustainability opportunities in industrial and commercial operations. The environmental costs of unplanned downtime extend far beyond lost productivity.
The Environmental Cost of Unplanned Downtime
When equipment stops unexpectedly, the restart process often consumes significantly more energy than steady operation. This energy spike contributes to higher carbon emissions and utility costs.
Material waste from interrupted processes can be substantial. Partial batches may require disposal, and in-progress work often needs to be scrapped when production lines halt unexpectedly.
Emergency support services deployed during downtime events typically involve expedited shipping, rush delivery charges, and sometimes helicopter or air freight transportation—all with substantial carbon impacts.
Strategies for Maximizing Equipment Uptime
Condition-based maintenance approaches monitor actual equipment health rather than following arbitrary schedules. This precision ensures interventions happen only when needed, maximizing uptime while minimizing wasted maintenance activities.
Integration with production scheduling allows maintenance to occur during planned downtime, eliminating additional disruptions. This coordination maximizes productive time and resource efficiency.
Rapid response protocols for sustainability-critical systems ensure that equipment affecting energy usage, emissions, or waste receives immediate attention when issues arise.
Beyond these remarkable technologies lies another powerful sustainability opportunity that’s often overlooked: the significant environmental benefits of minimizing equipment downtime.
Key Takeaways for Sustainable Maintenance
Smart maintenance represents a powerful but often overlooked sustainability opportunity. By implementing intelligent systems and processes, organizations can dramatically reduce their environmental footprint while improving operational performance and reducing costs.
The five pillars of sustainable maintenance—energy optimization, resource conservation, emissions reduction, waste minimization, and water conservation—provide a framework for organizations to assess and improve their maintenance practices. A comprehensive work order management system ties these efforts together, providing the data and workflow infrastructure necessary for success.
As technologies continue to evolve, the potential for maintenance to drive sustainability will only grow. Organizations that embrace these opportunities now will gain competitive advantages while contributing to a more sustainable future.
FAQS
How does computerized maintenance management directly impact an organization’s carbon footprint?
Computerized maintenance systems reduce carbon footprints by optimizing travel routes, preventing equipment inefficiencies, eliminating paper waste, and extending asset lifecycles through data-driven maintenance decisions.
How can preventive maintenance scheduling systems reduce resource consumption?
These systems minimize resource consumption by optimizing maintenance timing, preventing catastrophic failures that waste materials, reducing energy usage from inefficient equipment, and extending component lifecycles.
Can facility management software integration improve both sustainability and operational efficiency?
Absolutely! Integrated facility software provides visibility across systems, identifies efficiency opportunities, tracks sustainability metrics, and coordinates maintenance activities to minimize waste while maximizing productivity.