Getting the right electrical components matters for your business. These parts keep operations running smoothly across automation systems and industrial equipment. When electrical components fail, your entire operation can grind to a halt.
Yaskawa Parts are just one of the very viable and high-quality options that you can invest in when you are looking for electrical components for your business. Maintaining an accurate parts inventory helps ensure you get exactly what you need when ordering replacements, minimizing downtime and keeping production on schedule.
Why Precision in Parts Selection Matters
If you purchase components that don’t match your equipment specifications, you’ve essentially wasted both money and time. Smart business owners keep spares of all critical electrical parts — sometimes even multiple backups — to prevent extended downtime when failures occur.
Finding the right parts becomes straightforward when you maintain detailed records of the components your systems rely on. Here are some practical guidelines to help you select appropriate electrical parts for your business operations:
Guidelines for Selecting Electrical Components
1. Specification Verification
Know your numbers. When reordering parts, verify voltage, current, resistance, capacitance, and frequency requirements. For specialized components, document any unique parameters. Understanding these specifications ensures compatibility with your existing systems.
2. Manufacturer Reliability
Not all manufacturers are created equal. Research suppliers before committing to their electrical parts. Your operation’s reliability depends on component quality. Look for manufacturers that offer solid warranties and maintain good inventory levels. Smaller manufacturers might offer lower prices but could struggle to meet your supply demands.
3. System Compatibility
Electrical components rarely work universally across all systems. Ensure new parts integrate with your existing equipment. Off-brand components might save money initially but often create integration problems or fail prematurely under daily operational stress.
4. Physical Considerations
Dimensions and configurations matter significantly when selecting replacement parts. Document any unique physical requirements to ensure proper fit and function. Even minor variations can prevent proper installation or compromise performance.
5. Supply Chain Factors
While price matters, availability often proves more important in the long run. Established manufacturers typically offer better reliability and consistency. Consider negotiating supply contracts with trusted vendors—many will work with you to ensure consistent access to quality parts at fair pricing.
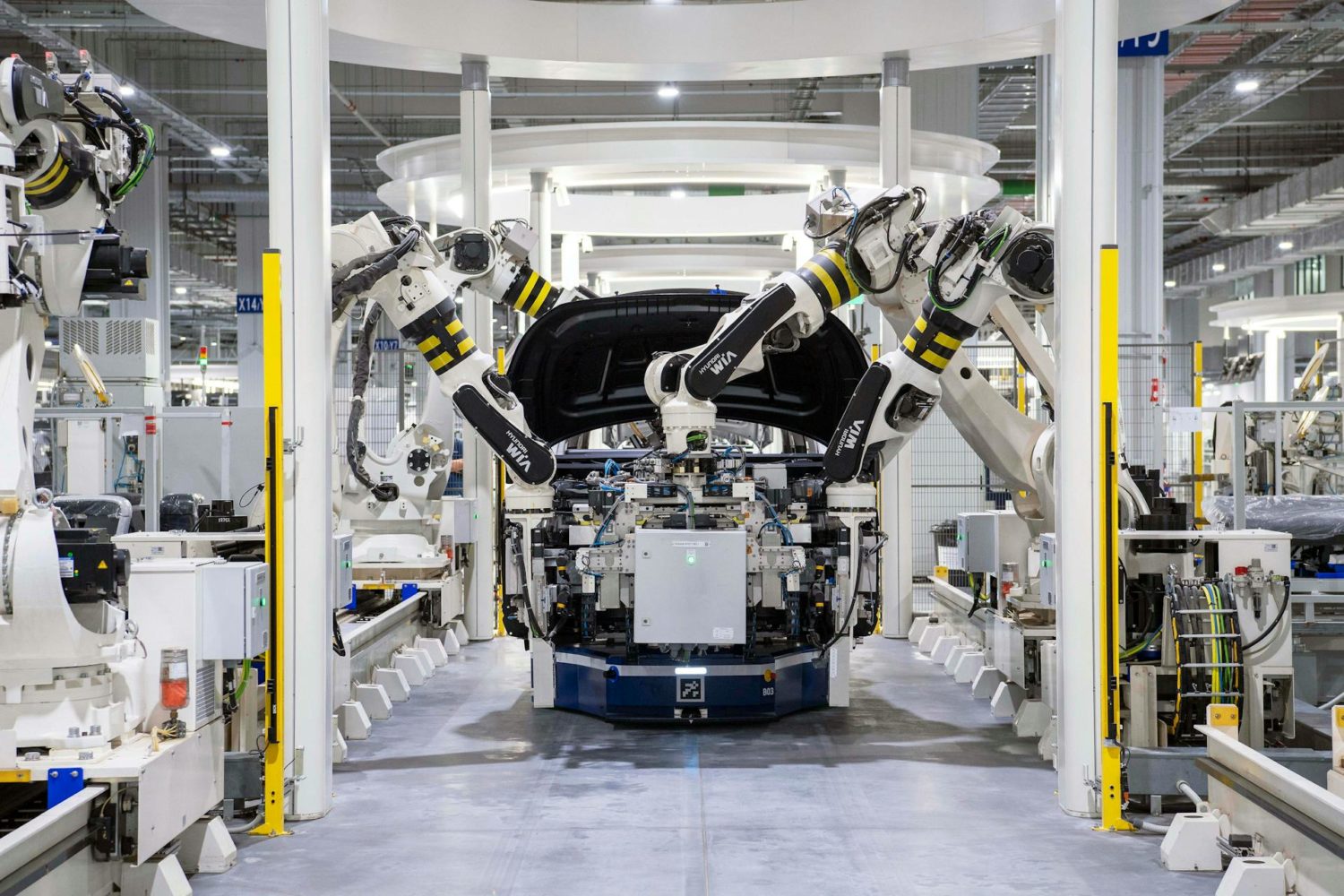
Accuracy: The Key to Successful Parts Management
Knowing exactly what you need when dealing with electrical components prevents costly mistakes. Maintain detailed records of each component’s specifications and performance history. This information, combined with a reliable supplier relationship, forms the foundation of effective parts management.
One-time suppliers seldom provide adequate support, consistent availability, or meaningful warranties. Ensuring your replacement parts match system requirements and can withstand operational demands prevents unexpected shutdowns due to poor inventory management or incorrect ordering.